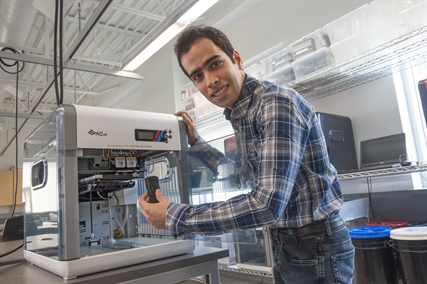
UBC Okanagan researcher discovers how 3D printing can be used in bone replacements
OKANAGAN – A new artificial bone design has been identified by a UBC Okanagan researcher.
Hossein Montazerian, a research assistant with UBC Okanagan’s School of Engineering, is examining the potential of artificial bones being made with a 3D printer.
According to a UBC Okanagan release issues today, Aug. 17, the new artificial bone design can be customized and made with a 3D printer for stronger, safer and more effective bone replacements.
Human bones are incredibly resilient, says Montazerian, but when things go wrong, replacing them can be a painful process, requiring multiple surgeries.
“When designing artificial bone scaffolds it’s a fine balance between something that is porous enough to mix with natural bone and connective tissue, but at the same time strong enough for patients to lead a normal life,” says Montazerian. “We’ve identified a design that strikes that balance and can be custom built using a 3D printer.”
Treating anything from traumatic fractures to defects is done using traditional bone grafting. This method requires moving bone from one part of the body to another, says the release. Unlike the traditional method, Montazerian says his artificial bone grafts, which can be custom printed to potentially fit any patient, would eliminate transplanting existing bone fragments.
After analyzing 240 different bone graft designs, Montazerian focused on ones that were porous and strong. The designs that performed the best were 3D printed and physical tests were run to determine how effective they would be in the real world.
“A few of the structures really stood out,” Montazerian adds. “The best designs were up to 10 times stronger than the others and since they have properties that are much more similar to natural bone, they’re less likely to cause problems over the long term.”
The release states that Montazerian and his collaborators are working on the next generation of designs that will use a mix of two or more structures.
“We hope to produce bone grafts that will be ultra-porous, where the bone and connective tissues meet and are extra-strong at the points under the most stress. The ultimate goal is to produce a replacement that almost perfectly mimics real bone.”
Before his bone graft designs can be used clinically, Montazerian says the technology still needs some advances. He says, for example, other researchers in the field are starting to refine biomaterials that won’t be rejected by the body and that can be printed with the very fine 3D details that his designs require.
“This solution has enormous potential and the next step will be to test how our designs behave in real biological systems,” he says. “I hope to see this kind of technology clinically implemented for real patients in the near future.”
Montazerian’s research was recently published in Science Direct's Materials & Design.
FYI contains information submitted from the public and is displayed exactly as it was received. Information is clearly attributed in bylines and not created by iNFOnews.ca staff. For more information, please contact the referring organization. If you have questions about FYI, or would like to submit information to FYI, please send directly to fyi@infonews.ca.
Join the Conversation!
Want to share your thoughts, add context, or connect with others in your community? Create a free account to comment on stories, ask questions, and join meaningful discussions on our new site.
Leave a Reply
You must be logged in to post a comment.